?What is a conveyor belt
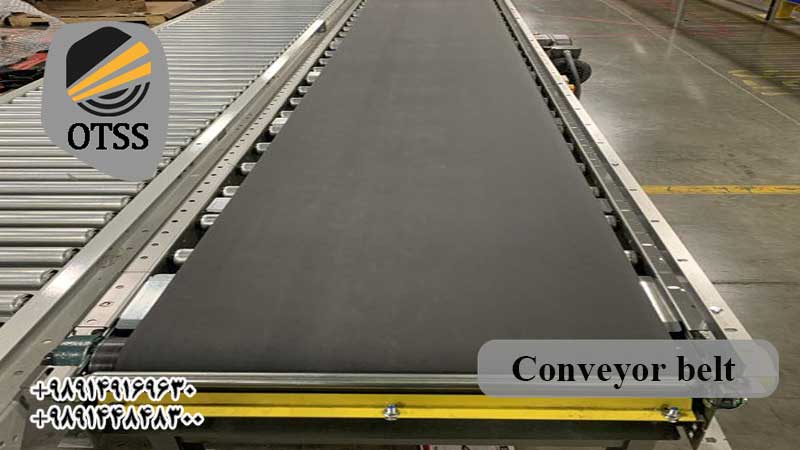
?What is a conveyor belt
A conveyor belt is a mechanical device used to transport materials from one location to another within a controlled path. It typically consists of a continuous belt made of rubber, metal, or fabric that is looped around two or more pulleys. One or more of these pulleys are powered by motors, which move the belt and the materials placed on it. Conveyor belts are integral to various industries and are used for transporting a wide range of products, from lightweight items like packages to heavy bulk materials such as rocks and minerals.
How Conveyor Belts Work
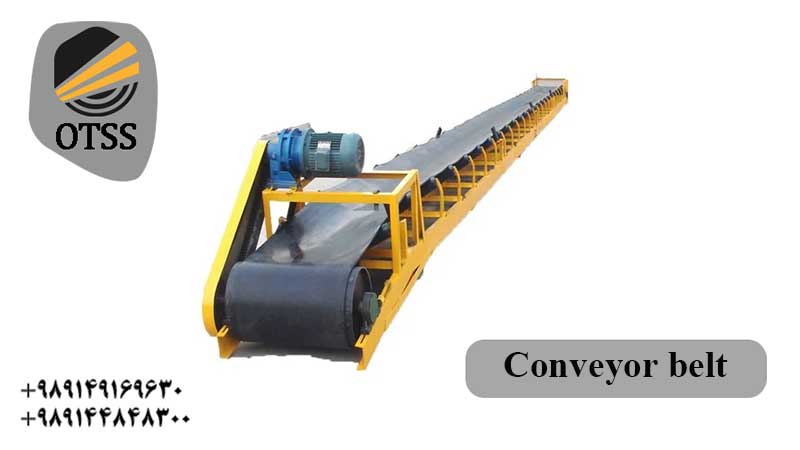
Conveyor belts function by creating a frictional force between the belt and the drive pulley. As the drive pulley rotates, it pulls the belt forward, allowing materials to move along the belt’s surface. Depending on the type and configuration, conveyor belts can move materials horizontally, inclined, or even vertically.
Types of Conveyor Belts
- Flat Belt Conveyor
The most common type, used for horizontal movement of items.
Suitable for handling products in manufacturing, packaging, and logistics
Sure! Here are some advantages and disadvantages of flat belt conveyors:
Advantages
?What is a conveyor belt
- Versatility: Flat belt conveyors can be used for a wide range of materials and are adaptable for different environments and industries.
- Simple and Cost-effective Design: They have a straightforward design, making them relatively inexpensive to manufacture and maintain.
- Smooth Surface: The smooth surface of flat belts is ideal for safely transporting delicate or fragile items.
- Easy to Clean: Many flat belt conveyors are simple to clean, which is advantageous for industries such as food processing.
- Reduced Spillage: With a continuous surface, there’s often less spillage compared to other conveyor types.
- Disadvantages
- Limited Incline Capability: Flat belt conveyors are not well-suited for inclines, as the lack of sidewalls can lead to product slipping when angles become too steep.
- Less Durability: Compared to other types like roller belt conveyors, flat belts can wear out faster.
- Material Limitations: They may not be ideal for heavy items or materials with sharp edges that can damage the belt.
- Limited Load Capacity: Flat belt conveyors generally have lower load capacities compared to some other types of conveyors.
- Tracking Issues: Belt tracking can be a concern; if the belt isn’t aligned properly, it can lead to misalignment and increased wear.
- These points should provide a clear overview of the pros and cons associated with flat belt conveyors. If you have further questions or need more detailed information, feel free to ask!
- .
- Modular Belt Conveyor:
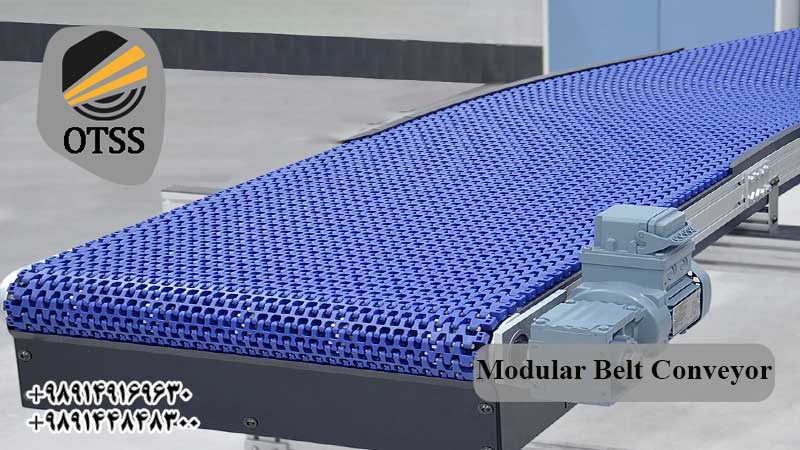
- Consists of interlinked segments, offering flexibility and ease of maintenance
- Often used in food processing and packaging industries
- Advantages and Disadvantages of Modular Conveyors
- Advantages:
- High Durability: Modular conveyors are made from robust materials such as plastic or stainless steel, making them highly resistant to wear and tear. This makes them ideal for heavy-duty or continuous operation in industrial environments.
- Customizable Design: Modular conveyors consist of interlocking modules, which allow for easy customization and adaptation to different conveyor lengths, widths, or shapes. This is particularly useful in industries with dynamic requirements.
- Easy Maintenance: Since the belts are made of individual modules, damaged sections can be easily replaced without requiring the entire belt to be replaced. This reduces downtime and maintenance costs.
- Enhanced Flexibility: The modular design enables conveyors to handle complex layouts, such as curves and inclines. They can be configured in a variety of ways, offering more flexibility compared to flat belt conveyors.
- Sanitary and Hygienic: Modular conveyors are often used in industries such as food processing due to their easy-to-clean design. The modular construction allows for thorough cleaning, reducing the risk of contamination.
- Non-slip Surface: The surface of modular belts often provides a better grip, reducing the risk of items slipping off, which is particularly useful when dealing with products on inclined surfaces.
- Variety of Applications: Modular conveyors can be used for various industries, including food and beverage, pharmaceuticals, and packaging, due to their versatility and durability.
- Disadvantages:
- Higher Initial Cost: Compared to simpler conveyor types like flat belt conveyors, modular conveyors tend to have a higher upfront cost due to the complexity of the modular design.
- More Complex Setup: While modular conveyors are highly customizable, they also require more time and technical expertise during installation, especially for complex layouts.
- Heavier Weight: The use of heavy-duty materials and the interlocking modular design can make modular conveyors bulkier and heavier than other types, which may increase transportation and setup challenges.
- Slower Speeds: Modular conveyors are generally slower than some other conveyor systems, such as roller conveyors, making them less suitable for applications requiring high-speed operations.
- Noise Levels: The interlocking design and heavier materials can create more noise during operation compared to other conveyor types, which could be a drawback in noise-sensitive environments.
- Maintenance of Moving Parts: Modular conveyors, while easy to repair, can still have numerous small moving parts that require regular inspection and upkeep to avoid malfunction.
- If you need further clarification or more detailed insights into how modular conveyors could fit into a specific application, feel free to ask!controlled path
- Cleated Belt Conveyor:
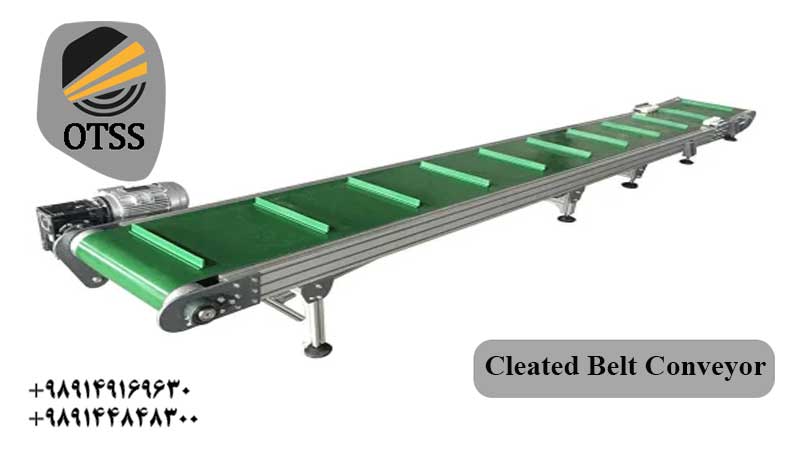
- Features raised edges or cleats to keep products in place.
- Ideal for transporting loose items or working on an incline.
- Here are the advantages and disadvantages of Cleated Belt Conveyors (also known as cleated or ribbed belt conveyors) in English:
- Advantages
- Prevents Material Slippage:
- Cleated belts are designed with raised edges (cleats) that prevent materials from slipping during transport, especially when the conveyor is inclined. This makes them ideal for moving items at steep angles.
- Efficient Transport of Bulk Materials:
- These conveyors are highly effective for transporting bulk materials such as grains, gravel, sand, or chemicals, as the cleats provide extra support for carrying loose or irregularly shaped items.
- Increased Load Capacity:
- The cleated design increases the load-carrying capacity of the conveyor because it can hold items more securely, ensuring better use of the belt’s surface area.
- Suitable for Inclined Conveying:
- Cleated belt conveyors are perfect for moving materials up or down inclined planes where flat belts would not be able to hold the material in place.
- Versatility in Industry Use:
- These conveyors are used in a variety of industries including agriculture, food processing, mining, and packaging, as they are effective in handling different types of products, including fragile items.
- Customizable Design:
- Cleated conveyors can be designed with different cleat shapes, sizes, and patterns to suit specific product requirements. This versatility allows for optimization based on the material type and production processes.
- Durability:
- Cleated belts are often made from durable materials like rubber or PVC, which can withstand harsh operating conditions such as exposure to moisture, chemicals, or abrasives.
- Disadvantages
- Higher Cost:
- Cleated belt conveyors can be more expensive compared to flat belt conveyors due to the additional material and complexity in their design. The inclusion of cleats increases manufacturing and maintenance costs.
- Increased Maintenance:
- The presence of cleats means more parts to wear out over time. If cleats become damaged or detached, the belt may need frequent maintenance or replacement, leading to potential downtime.
- Limited to Specific Materials:
- While cleated belts are great for bulk and uneven materials, they may not be as suitable for products that require a smooth, continuous surface, such as sensitive items that could get caught between the cleats.
- Potential for Product Damage:
- Some fragile materials may be damaged by the cleats themselves, especially if the cleats are not appropriately sized or shaped for the product being transported.
- Noise Generation:
- The added friction and movement caused by the cleats can result in higher noise levels during operation, especially at high speeds. This could be a drawback in environments where noise reduction is essential.
- Weight Limitations:
- While cleats improve the belt’s ability to transport materials at an incline, there are still limitations on how much weight can be carried before the belt slips or breaks.
- Reduced Conveyor Speed:
- Cleated conveyors tend to operate at lower speeds compared to flat belt conveyors, as higher speeds could lead to increased wear on the cleats and cause instability for the items being transported.
- Conclusion
- Cleated belt conveyors are highly effective in industries that require inclined transport and the secure handling of bulk materials. However, their higher cost, increased maintenance needs, and some limitations in terms of speed and noise should be considered before implementation. These conveyors are ideal when the benefits of secure material handling outweigh the potential downsides.
- If you’d like more detailed information on how cleated conveyors can be applied in a specific industry or scenario, feel free to ask!
- Incline/Decline Belt Conveyor:
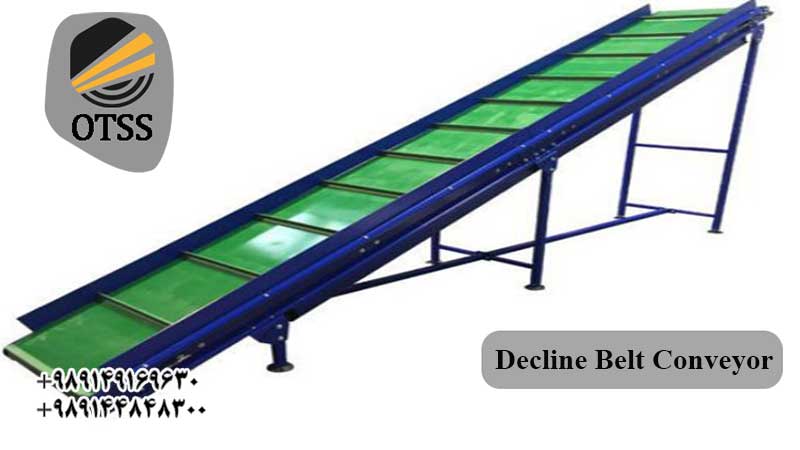
- Designed for moving materials between different elevations.
- Widely used in distribution centers and warehouses.
- Here are the advantages and disadvantages of Incline/Decline Belt Conveyors in English:
- Advantages:
- Efficient Material Handling on Inclines/Declines:
- Incline and decline belt conveyors allow materials to be easily moved between different elevations, which is essential in environments with multiple floors or elevated workstations. They are particularly useful in production lines where vertical space needs to be utilized.
- Reduction in Manual Labor:
- These conveyors automate the movement of materials vertically, reducing the need for manual lifting and transport. This not only improves efficiency but also helps minimize the risk of workplace injuries related to heavy lifting.
- Flexibility in Design:
- Incline/decline conveyors can be customized with various belt materials (e.g., rubber, PVC) and cleats to suit different types of materials. They can be adapted to handle different inclines/declines, ensuring that materials remain secure during transport.
- Space-saving:
- By utilizing vertical space, these conveyors save valuable floor space in industrial settings. This can be especially advantageous in compact facilities where efficient space utilization is critical.
- Wide Range of Applications:
- Incline/decline conveyors are used in diverse industries such as food processing, packaging, warehousing, and mining. They are versatile and can transport various materials, from small parts to bulk goods.
- Smooth and Controlled Movement:
- With proper belt tension and cleats, incline/decline conveyors can provide smooth, controlled movement of materials, reducing the risk of product damage.
- Supports Continuous Production Flow:
- These conveyors help maintain a continuous flow in the production process by efficiently moving materials between workstations or storage areas, ensuring that production lines do not experience delays due to manual material handling.
- Disadvantages:
- Higher Initial Cost:
- Incline/decline belt conveyors are more complex to design and install compared to flat belt conveyors. The need for additional components, such as cleats or sidewalls, and custom configurations for inclines can lead to higher upfront costs.
- Increased Wear and Tear:
- The mechanical strain placed on the belt and components during inclined or declined transport can lead to increased wear. Belts are subject to greater stress when moving materials against gravity, which can reduce their lifespan.
- Potential for Material Slippage:
- Without the right cleats or friction surface, materials may slip down the belt when the incline angle is too steep. This is particularly true for smooth or slippery materials, which may not have enough grip on the belt.
- Power Consumption:
- Incline/decline conveyors require more power to move materials, especially when transporting heavier loads upward. This can result in higher energy costs compared to horizontal conveyors.
- Maintenance and Downtime:
- Because incline/decline conveyors are exposed to more wear, they may require more frequent maintenance. This includes checking belt tension, replacing worn cleats, and ensuring the belt remains properly aligned. Any issues can lead to downtime in the production line.
- Limited Speed for Steep Inclines:
- When dealing with steep inclines, conveyor speeds must often be reduced to ensure material stability and prevent items from slipping or shifting during transport. This can reduce overall throughput in high-speed production environments.
- Weight and Load Limitations:
- Incline/decline conveyors may struggle with extremely heavy or bulky items, particularly when moving materials upwards. The additional gravitational forces can increase the strain on the system, potentially leading to mechanical failures or system inefficiencies.
- Conclusion:
- Incline/decline belt conveyors are highly efficient for transporting materials between different elevations, offering several advantages like space-saving, improved safety, and versatile applications. However, their higher cost, increased wear, and the need for frequent maintenance must be considered. These conveyors are most beneficial in settings where the advantages of efficient vertical transport outweigh the potential drawbacks.
- If you need more specific advice on how these conveyors might work for your specific industry or setup, feel free to ask!
- Curved Belt Conveyor:
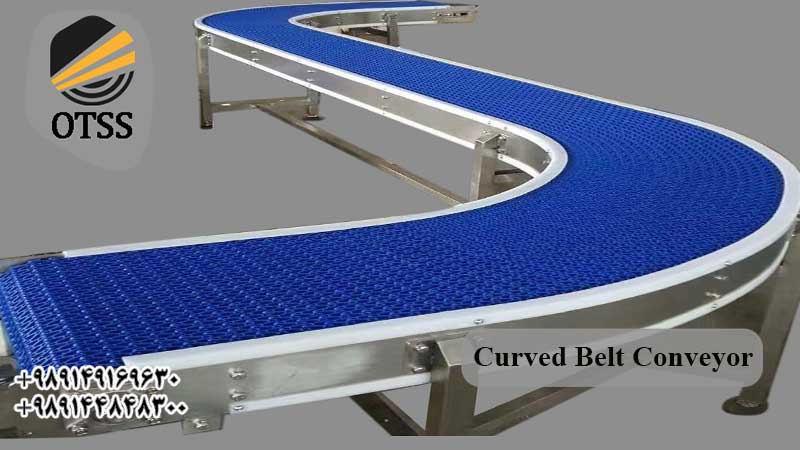
- Enables products to be moved along a curved path.
- Useful for fitting conveyors into tight spaces.
- Certainly! Here’s an overview of the advantages and disadvantages of curved conveyors:
- Advantages
- Space Efficiency:
- Curved conveyors allow for efficient space utilization by routing around obstacles and fitting into complex layouts without requiring additional transfer points.
- Smooth Transition:
- They provide a seamless transition between different conveyor sections, reducing the need for manual intervention and maintaining product orientation.
- Reduced Handling
- By eliminating the need for additional conveyors at corners or junctions, curved conveyors minimize material handling and reduce potential damage to products.
- Versatility:
- Suitable for various industries, including manufacturing, distribution, and packaging, curved conveyors can handle a wide range of products such as boxes, luggage, or loose items.
- Aesthetic Appeal:
- They offer a clean and organized look, especially in environments where layout visibility and order are essential, such as airports or retail facilities.
- Disadvantages
- Complex Design and Construction:
- Curved conveyors often require more complex design and construction, leading to higher initial costs compared to straight conveyors.
- Maintenance Challenges:
- The curve sections can introduce additional maintenance challenges, particularly with belt tension and tracking.
- Speed Limitations:
- Due to centrifugal forces, there may be speed limitations to prevent products from sliding off when navigating curves.
- Installation Complexity:
- Installing a curved conveyor can be more complex and time-consuming, often requiring specialized knowledge and additional equipment.
- Higher Power Consumption:
- The motors and drives may need to exert more power, especially on tight curves, which can lead to increased energy consumption.
- These factors should be carefully considered when deciding whether a curved conveyor is the right choice for your specific application.
?What is a conveyor belt
- Roller Conveyor:
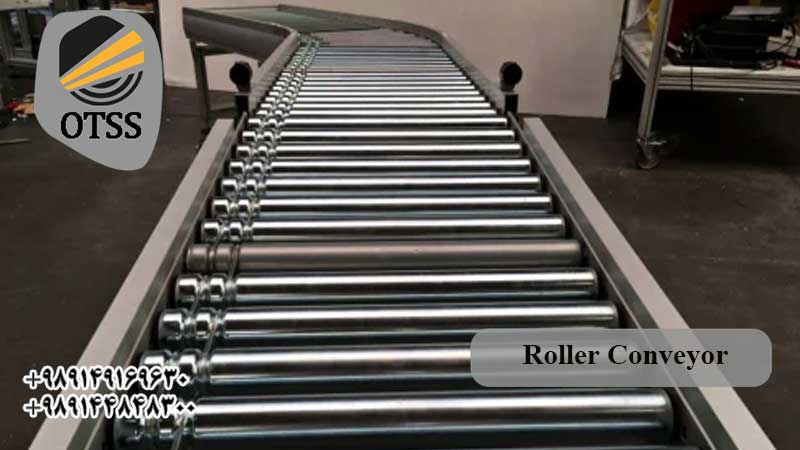
- Uses a series of rollers instead of a continuous belt.
- Typically used for moving heavy loads like pallets.
- Here’s an analysis of the advantages and disadvantages of roller conveyors:
- Advantages
- Cost Efficiency:
- Roller conveyors, especially gravity-driven models, are generally more cost-effective compared to powered conveyor systems. This makes them ideal for applications where simple product movement is required without extensive automation.
- Versatility:
- They are versatile and can handle a wide variety of products, from small packages to large containers, making them suitable for different industries such as manufacturing, warehousing, and logistics.
- Modularity:
- Roller conveyors can be easily reconfigured or expanded based on the changing needs of the operation. This modularity allows for easy addition of new sections or changing layouts with minimal disruption.
- Low Maintenance:
- Due to their simple construction, roller conveyors usually require less maintenance compared to other conveyor types. Components can be replaced individually, reducing downtime and maintenance costs.
- Energy Efficiency:
- Gravity roller conveyors do not require power, making them energy-efficient and environmentally friendly. This also reduces operational costs when compared to powered conveyors.
- Gentle Handling:
- Roller conveyors can provide smooth and gentle handling of fragile items, making them ideal for transporting delicate goods such as glassware or electronics.
- Flexibility in Speed:
- Speed can be adjusted by changing the pitch of the rollers or by adding a braking system. This allows operators to control the flow of items through the system.
- Disadvantages
- Limited Product Types:
- Roller conveyors are not suitable for irregularly shaped, very small, or very soft items as these can get stuck between rollers or cause jams.
- Risk of Product Damage:
- If not properly configured, products can accumulate on rollers, leading to jams, backpressure, or even product damage. This is especially true for items that have varying weights or sizes.
- Inconsistent Flow:
- Gravity roller conveyors rely on gravitational force, which can lead to inconsistent flow speeds, especially for lightweight products. This might necessitate additional manual handling.
- Noise:
- Depending on the material of the rollers and the weight of the products, roller conveyors can become noisy, which might not be ideal for certain environments like offices or assembly lines where noise reduction is a priority.
- Complex Installation for Long Systems:
- While small sections are easy to install, longer and more complex systems can require precise alignment to ensure smooth operation, making installation more time-consuming and costly.
- Limited Incline Capability:
- They are less effective for inclined transport compared to belt conveyors, as rollers provide less friction. This can limit their use in applications requiring significant elevation changes.
- Considering these points, roller conveyors are ideal for straightforward transport and accumulation applications but may require additional considerations for more complex or sensitive operations.
?What is a conveyor belt
Advantages of Conveyor Belts
- Increased Efficiency: Conveyor belts streamline operations by automating material transport, reducing labor costs.
- High Load Capacity: Capable of transporting heavy and bulky materials over long distances.
- Versatility: Can be tailored to handle different types of products and work in various environments.
- Improved Safety: Minimizes the risk of manual handling injuries by automating transport.
?What is a conveyor belt
Disadvantages of Conveyor Belts
- High Initial Cost: Installation and setup of conveyor belt systems can be expensive.
- Space Requirements: Conveyor belts can require significant space depending on the application.
- Limited Flexibility: Once installed, modifying the system layout can be challenging.
- Maintenance Needs: Regular maintenance is necessary to ensure smooth operation and longevity.
Common Applications of Conveyor Belts
- Manufacturing: Used in assembly lines and automated production processes.
- Mining: Essential for transporting extracted minerals and ores.
- Food Processing: Maintains hygiene standards while handling food items.
- Logistics & Warehousing: Facilitates sorting and distributing goods in large facilities.
- Agriculture: Used for transporting grains, seeds, and other bulk agricultural products.
Frequently Asked Questions (FAQs)
- What is a conveyor belt made of?
Conveyor belts are typically made of materials like rubber, fabric, PVC, polyurethane, and sometimes metal, depending on the application requirements. - How long do conveyor belts last?
The lifespan of a conveyor belt depends on the material, frequency of use, and operating conditions. A well-maintained conveyor belt can last for several years. - What industries use conveyor belts?
Conveyor belts are used in various industries including mining, food processing, manufacturing, logistics, packaging, and more. - How can conveyor belt efficiency be improved?
Efficiency can be improved by choosing the right belt material, ensuring proper alignment, regular maintenance, and using energy-efficient motors. - ?What is a conveyor belt
Maintenance and Repair Tips
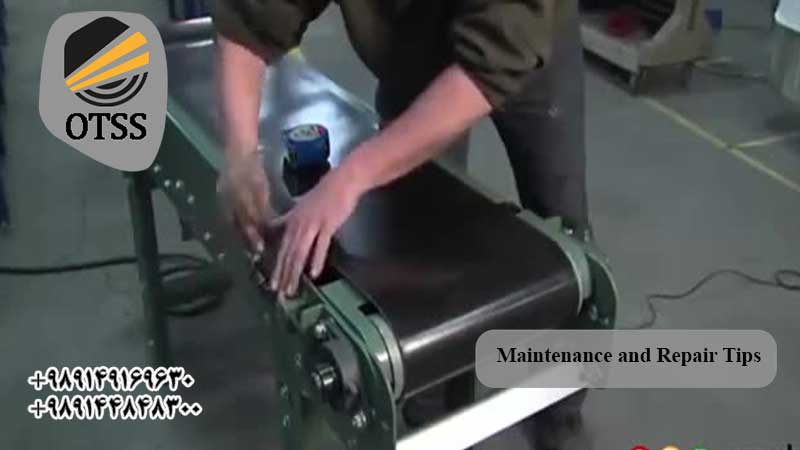
- Regular Inspections:
- Conduct visual and mechanical inspections to detect wear and tear, misalignment, and loose components.
- Belt Tension and Tracking:
- Proper tension and alignment are crucial for preventing slippage and ensuring smooth operation.
- Lubrication:
- Keep moving parts like rollers and bearings well-lubricated to reduce friction and extend lifespan.
- Cleaning and Debris Removal:
- Regularly clean the belt and remove any debris to prevent damage and maintain hygiene, especially in food processing industries.
- Replace Worn-out Parts:
- Timely replacement of worn parts like rollers, pulleys, and belts prevents unexpected downtime.
- Emergency Stop Systems:
- Ensure that emergency stop systems are operational to prevent accidents and minimize damage in case of malfunctions.
- ?What is a conveyor belt
Conclusion
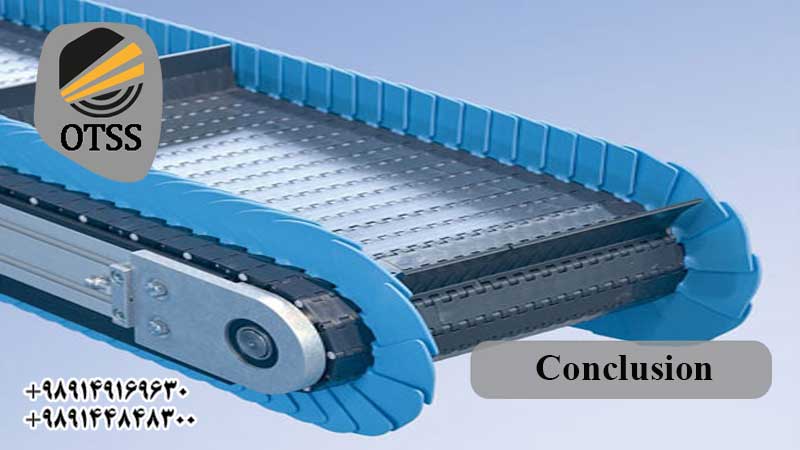
Conveyor belts are critical components in industrial automation, enhancing productivity and operational efficiency across various industries. Understanding the types, applications, and proper maintenance strategies is essential to maximize the value and performance of these systems. With the right care and configuration, conveyor belts can serve as a reliable and efficient solution for material handling needs.
Conveyor belts are crucial components in a wide range of industries for efficiently moving materials. Proper maintenance and repair are essential to ensure they operate smoothly, prevent unexpected downtimes, and extend their lifespan. Here are some key aspects of conveyor belt maintenance and repair:
Regular Inspections
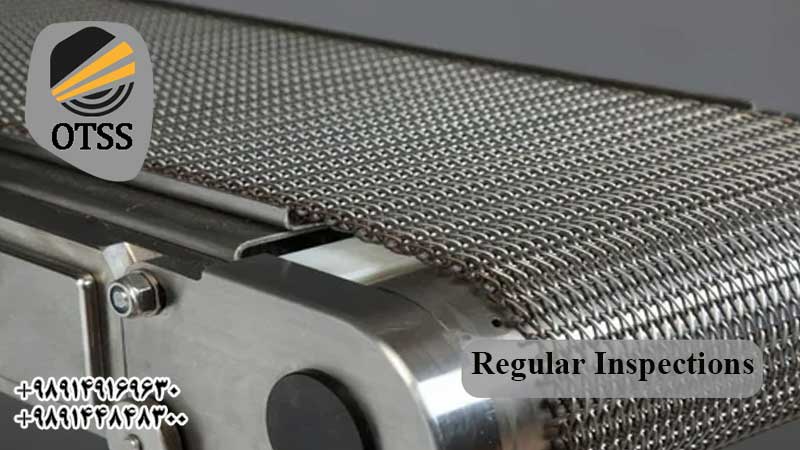
- Visual Inspection: Regularly check for signs of wear and tear, such as fraying edges, cracks, or worn spots on the belt.
- Check for Misalignment: Ensure the conveyor belt is running straight and is properly aligned, as misalignment can cause excessive wear.
- Inspect Belt Tension: Proper tensioning is essential to prevent slippage or excessive strain on the belt.
?What is a conveyor belt
Maintenance Tips
- Cleaning: Regularly clean the conveyor belt and its components to remove debris and prevent buildup that can cause damage.
- Lubrication: Proper lubrication of moving parts like bearings and rollers can reduce friction and wear.
- Check Pulley and Rollers: Ensure that pulleys and rollers are in good condition and replace any that are worn or damaged.
- Belt Condition: Examine the surface for any damages, and repair minor damages quickly to avoid further degradation.
Repair Procedures
- Patch Repair: For small punctures or damages, use belt repair patches to cover and protect the damaged area.
- Vulcanization: This is a process of using heat and pressure to repair larger tears or rips, which can be done with hot or cold vulcanization methods.
- Splice Repair: If the splice (joint where two ends of the belt are connected) is damaged, it may need to be redone.
Safety Considerations
- Always ensure the conveyor system is turned off and properly locked out before performing maintenance.
- Use appropriate personal protective equipment (PPE) during maintenance and repairs.
Regular Maintenance Schedule
- Establish a routine maintenance schedule to inspect and service the conveyor belt system.
- Keep detailed maintenance records to track the condition and any issues over time.
By following these guidelines, you can help ensure that conveyor belts remain reliable and efficient parts of your operation.